Welcome to the comprehensive guide on exploring the Amazon Warehouse in Atlanta! In this article, we will take an in-depth look at the operations, layout, safety measures, and sustainability initiatives of this massive facility. Whether you are a curious visitor or someone interested in the inner workings of one of the world’s largest warehouses, this guide has got you covered.
Understanding the Amazon Warehouse Operations
When it comes to the operations of the Amazon Warehouse in Atlanta, efficiency is key. To achieve this, a combination of cutting-edge technology and human expertise is employed.
Before we begin: Every Amazon Seller needs a suite of tools for Keyword Research, Product Development, and Listing Optimization. Our top pick is Helium 10 and readers of this post can get 20% off their first 6 months by clicking the image below.
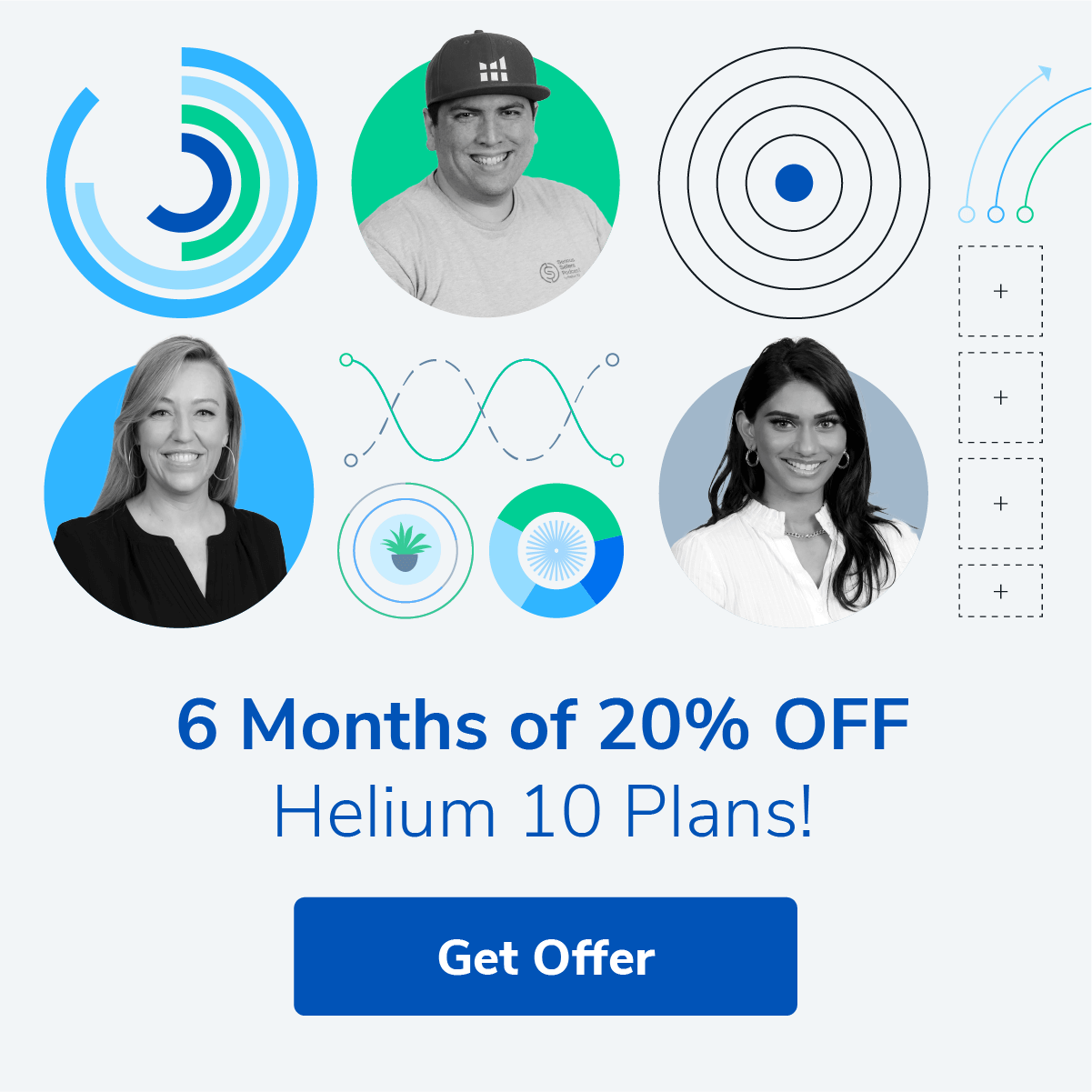
The Amazon Warehouse in Atlanta is a bustling hub of activity, with workers and machines working in harmony to ensure that orders are processed and shipped with precision and speed. Let’s take a closer look at the various aspects of this operation.
The Role of Robotics in Amazon Warehouse
One of the standout features of the Amazon Warehouse in Atlanta is the extensive use of robotics. These autonomous machines tirelessly work hand in hand with human workers to streamline the various processes involved in managing inventory, picking, and packing orders.
The robots, equipped with advanced sensors and algorithms, navigate the warehouse floor with ease, efficiently moving from one location to another. They are capable of lifting and transporting heavy items, reducing the physical strain on human workers. With their precision and speed, these robots have significantly increased the productivity of the warehouse.
Furthermore, the robots are constantly learning and adapting, thanks to artificial intelligence. They can analyze data and make real-time decisions, optimizing the flow of goods within the warehouse. This ensures that items are always readily available for order fulfillment, minimizing delays and improving customer satisfaction.
The Human Element in Warehouse Operations
While robotics play a vital role in the warehouse, the human workforce is equally important. Skilled employees ensure that the entire operation runs smoothly and efficiently. From overseeing logistics to maintaining quality control, these individuals are integral to the success of Amazon’s operations.
Human workers collaborate with the robots, working side by side to ensure that every order is accurately picked, packed, and shipped. They are responsible for monitoring the robots’ performance, troubleshooting any issues that may arise, and making critical decisions that require human judgment.
Additionally, human workers bring a level of adaptability and problem-solving skills that cannot be replicated by machines. They are quick to identify and resolve any issues that may occur during the fulfillment process, ensuring that customers receive their orders in perfect condition and on time.
Inventory Management at Amazon Warehouse
Accurate inventory management is crucial for the seamless functioning of the Amazon Warehouse. With millions of items stored and shipped daily, advanced systems are in place to track and organize inventory. This ensures that customers receive their orders promptly, while minimizing errors and delays.
The warehouse employs state-of-the-art barcode scanning technology and RFID (Radio Frequency Identification) tags to keep track of every item in real-time. This allows for precise inventory counts and efficient replenishment of stock. The data collected is constantly analyzed to identify trends and optimize storage strategies, ensuring that popular items are readily available for quick shipment.
Moreover, the inventory management system is integrated with the order fulfillment process, enabling seamless coordination between picking, packing, and shipping. This integration ensures that items are accurately picked from the shelves, packed securely, and shipped to the right destination.
By employing a combination of technology and human expertise, the Amazon Warehouse in Atlanta has revolutionized the way goods are stored, managed, and shipped. The efficient collaboration between robots and human workers, coupled with advanced inventory management systems, has enabled Amazon to meet the ever-increasing demands of its customers while maintaining high standards of quality and efficiency.
The Layout of Amazon Warehouse in Atlanta
Now that we have a glimpse of the operations, let’s delve into the layout of the Amazon Warehouse in Atlanta.
The Amazon Warehouse in Atlanta is a sprawling facility that is meticulously designed to optimize efficiency and productivity. The layout of the warehouse is carefully planned, taking into consideration the various stages of the fulfillment process.
The Receiving Area
The first stop for incoming merchandise is the receiving area. This area is bustling with activity as shipments from various suppliers arrive throughout the day. The warehouse has a dedicated team of trained personnel who work diligently to sort and inspect each shipment for quality. Specialized equipment, such as conveyor belts and barcode scanners, are used to streamline the receiving process. Any damaged or defective items are identified and set aside for further inspection or return.
Once the shipments are sorted and inspected, they are ready to be prepared for storage and distribution. The receiving area is equipped with state-of-the-art technology that ensures accurate inventory management. Each item is carefully logged into the warehouse management system, allowing for real-time tracking and efficient retrieval when needed.
The Stowing Area
Once received, items are systematically stowed in designated areas within the warehouse. The stowing area is a well-organized space with shelves, racks, and bins that are strategically arranged to maximize storage capacity. The warehouse utilizes an optimal storage system that takes into account factors such as item size, weight, and demand frequency. This system ensures that popular items are easily accessible, reducing the time and effort required to retrieve them during the picking stage.
The stowing process is carried out by trained warehouse associates who follow strict guidelines to ensure accurate placement of items. Advanced technology, such as automated guided vehicles (AGVs), assists in the stowing process, ensuring items are placed in the correct location. This meticulous attention to detail in the stowing area minimizes errors and facilitates efficient inventory management.
The Picking and Packing Area
The picking and packing area is where the magic happens. This bustling section of the warehouse is a hive of activity, with employees and robots working together to fulfill customer orders. The utilization of advanced algorithms and machine learning technology ensures that picking routes are optimized, reducing time and effort required to complete each order.
Warehouse associates, equipped with handheld devices or wearable technology, receive real-time instructions on the items to be picked. They navigate through the aisles, guided by the most efficient route suggested by the system. Collaborative robots, known as “cobots,” work alongside the associates, assisting in picking heavy or bulky items. These cobots are equipped with sensors that enable them to safely navigate through the warehouse and interact with humans.
Once the items are picked, they are meticulously packed in the packing area. Associates carefully select the appropriate packaging materials, taking into account factors such as size, weight, and fragility of the items. The packing process is carried out with utmost precision, ensuring that each package is securely sealed and protected. Special attention is given to fragile items, with additional cushioning and protective measures implemented to prevent any damage during transit.
The Shipping Area
At the final stage of the fulfillment process, the shipping area takes center stage. This area is a hub of activity, with packages being organized, labeled, and loaded onto trucks for transportation. The shipping area is equipped with advanced logistics software that optimizes the shipping process. Each package is assigned the most efficient shipping route, taking into consideration factors such as destination, package size, and delivery time requirements.
The warehouse utilizes automated sorting systems that efficiently route packages to the appropriate loading docks. Conveyor belts, barcode scanners, and automated labeling machines streamline the shipping process, ensuring accurate and timely dispatch of packages. Associates work diligently to ensure that each package is properly labeled with the correct shipping information, minimizing the chances of any errors or delays.
Once the packages are loaded onto trucks, they embark on their journey to their final destinations. The warehouse’s strategic location, coupled with efficient logistics management, ensures fast and reliable delivery to customers across the region.
The layout of the Amazon Warehouse in Atlanta is a testament to the company’s commitment to excellence in fulfillment operations. Every aspect of the warehouse’s design and organization is geared towards maximizing efficiency, accuracy, and customer satisfaction. From the receiving area to the shipping area, each stage of the fulfillment process is carefully orchestrated to ensure that products are handled with care and delivered seamlessly to customers.
Safety Measures in Amazon Warehouse
Ensuring the safety of all employees and visitors is a top priority for Amazon Warehouse in Atlanta. Let’s explore the safety measures in place.
Safety Training for Employees
Prior to joining the warehouse team, employees undergo comprehensive safety training. This equips them with the knowledge and skills necessary to handle equipment, follow safety protocols, and respond effectively in emergency situations.
Safety Equipment and Protocols
A wide range of safety equipment, such as personal protective gear and ergonomic tools, is provided to employees. Regular safety inspections and audits are conducted to ensure compliance with safety protocols and identify areas for improvement.
Emergency Response Plan
Amazon Warehouse in Atlanta has a well-defined emergency response plan in place. This includes detailed evacuation procedures, emergency exits, and designated assembly points. Regular drills are conducted to ensure that everyone is prepared in the event of an emergency.
Sustainability Initiatives at Amazon Warehouse
Amazon is committed to reducing its environmental impact and the Atlanta Warehouse plays its part in this effort.
Energy Efficiency Measures
The facility incorporates various energy efficiency measures, such as LED lighting and smart heating and cooling systems. These initiatives not only reduce energy consumption but also contribute to cost savings and a greener footprint.
Waste Management Strategies
To minimize waste, the Amazon Warehouse in Atlanta implements robust waste management strategies. Recycling programs are in place, ensuring that materials like cardboard, plastic, and paper are handled responsibly.
Green Packaging Solutions
Amazon actively explores and implements innovative green packaging solutions. From using biodegradable materials to optimizing packaging design for minimal waste, the warehouse takes steps to reduce its environmental impact.
That wraps up our comprehensive guide to exploring the Amazon Warehouse in Atlanta. We hope this article has provided valuable insights into its operations, layout, safety measures, and sustainability initiatives. Whether you’re intrigued by the cutting-edge technology, the dedication of the workforce, or the commitment to environmental responsibility – the Amazon Warehouse in Atlanta offers an impressive behind-the-scenes experience.
Enhance Your Amazon Selling Experience
As you’ve explored the inner workings of the Amazon Warehouse in Atlanta, it’s clear that innovation and efficiency are at the forefront of Amazon’s operations. If you’re an Amazon Seller looking to bring the same level of sophistication to your business, Your eCom Agent is here to help. With our AI-powered tools, you can effortlessly develop better products, analyze customer feedback, and optimize your detail pages. Embrace the power of AI and subscribe to Your eCom Agent’s AI Tools today to transform your Amazon selling experience!